Dryer / Cooler
Vacuum Mixing Dryer - VTH The batch-contact dryer for form-stabilized drying
under vacuum. For the efficient drying of powders, granules, carbon black and pigments. Advantages / features: Technical Data:
Batch
size: |
 |
500 to 10'000 liter
(132 to 2642 US gal.) |
Temperature: |
|
up to 180ºC (356ºF) |
Vacuum: |
|
up to –0.98
bar (-14.2 psi) |
Leakrage rate: |
|
<15mbar/h (<0.22psi/h)
at max. vacuum |
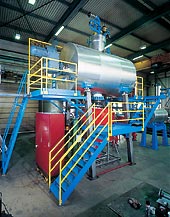
MDI-Prepolymer-Plants
MDI-Prepolymer-Production Plant MDI-Storage
and Conveying System: Includes a high precision reliable temperature control system, agitator, and all required controls
and safety components.
Reactor: 3 to 12 m3 (106 to 424 ft3), stainless steel, operating pressure from vacuum to
2 bar (29 psi), includes mixing tool and all required controls and safety components.
Prep-Storage Tank: 12 to 24
m3 (424 to 847 ft3), stainless steel, operating pressure 2 bar (29 psi).
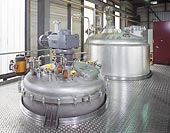
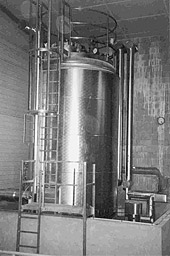
Magna Drum Transport and storage
container to maintain a constant temperature of liquid to pasty products, as well as melting.
Technical data:
Nominal
volume: |
|
1’100
l (290 gal.) |
Interior
diameter: |
 |
1.08
m (42.5 in.) |
Length/width
(base): |
|
1.22
m (48.0 in.) |
Total
height: |
|
1.60
m (63.0 in.) |
With
base |
Material: carbon steel / stainless steel With
40mm insulation and electric heating Adjustable thermostat to maintain the given temperature setting.
Options: Inert
gas connection Without heating
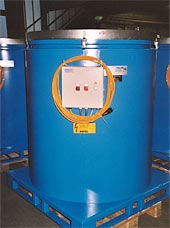
Competence and
performance from one source
• |
Carrying out of project
studies based on your data (e.g. need of raw material and production capacities) |
• |
Support during the
fixing of the production methods by our industry proven process engineering |
• |
Planning and layout
for the storage, drying, conveying and dosing of raw materials and intermediate products, the real production and the filling |
• |
Determination of the
capacities and optimum production units |
• |
Layout of electrical
and hydraulic systems |
• |
Calculation of conveying
performances |
• |
Set up of the total
need of electrical energy, cooling water, nitrogen, etc. The result is the energy balance. |
• |
Design and development
of controls based on PLC or PC |
• |
Determination of the
sensors and the metrology |
• |
Tests of your recipes
on our own test systems |
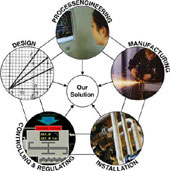
Upon request,
we will provide references of plants that we designed, manufactured and put into operation for the following product categories:
• High-viscosity adhesives • High-viscosity sealants • Athletic field and floor
coatings • PVC-Plastisoles • Putties • Varnishes and paints • Epoxies and binding compounds •
Transfer and storage of MDI • Powders drying • Vacuum drying • Storing, transferring and filling
of high-viscosity products
|